Nitrosamine Drug Substance-Related Impurities (NSDRIs) are probable human carcinogens that have become a critical concern in pharmaceutical formulations, prompting recalls and stringent oversight by regulatory authorities due to potential health risks. As regulations continue to evolve, drug manufacturers are required to adopt comprehensive, proactive strategies to mitigate nitrosamine contamination in their products from all potential sources.
Aptar CSP’s N-Sorb technology is designed to address this need by actively preventing nitrosamine formation, reducing nitrosamine amounts and growth rates over shelf life, and maintaining nitrosamine levels within regulatory limits, especially during storage and transport. The technology provides continuous protection against nitrosamine formation throughout the drug product’s lifecycle, from pre-production to patient use. This ensures compliance with regulatory limits and protects product integrity, reducing potential recalls or regulatory actions.
What is N-Sorb?
N-Sorb leverages our 3-Phase Activ-Polymer™ platform technology to deliver continuous protection against nitrosamine formation throughout the drug product’s lifecycle, from production to patient use. The platform technology, which can be deployed in physical formats ranging from extruded film to molded polymer pieces, incorporates active chemistries into a polymer matrix to provide moisture control, gas scavenging, microbial pathogen reduction, and aroma reduction or emission. Currently trusted by leading brands to protect sensitive APIs from degradation and/or oxygen exposure, this technology has been re-engineered to address nitrosamine formation.
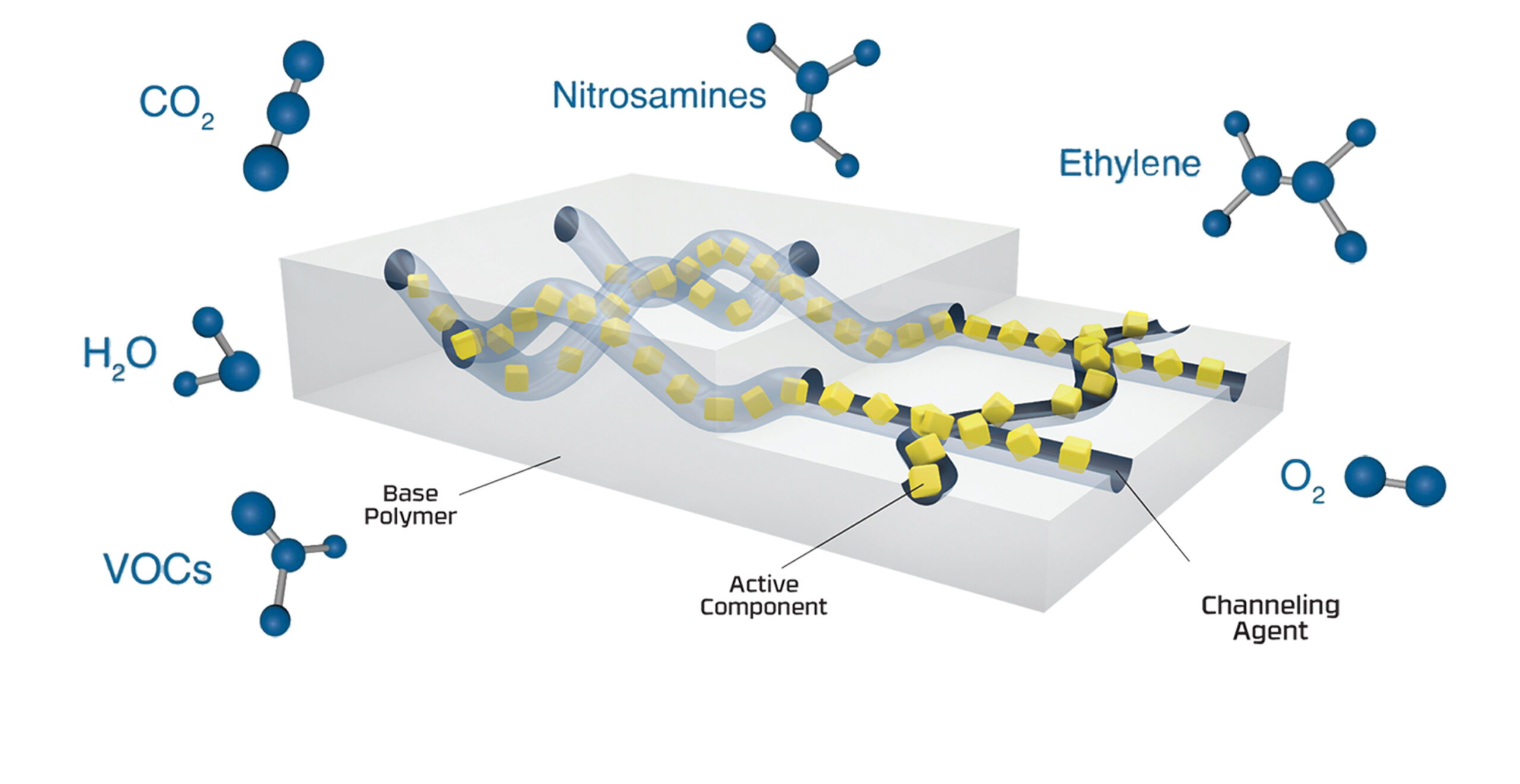
How does N-Sorb Mitigate Nitrosamine Risks?
N-Sorb technology’s intelligent design allows it to react with nitrosamine precursors in the packaging headspace to inhibit nitrosamine formation as well as scavenge nitrosamine impurities post-formation.
Preventing Nitrosamine Formation:
Nitrosamines form when certain precursors, like nitrites (or other generated nitrosating agents), react with secondary or tertiary amines in the drug formulation. N-Sorb captures and removes these nitrosamine precursors from the packaging’s headspace before they can react. By scavenging, reacting with, or otherwise removing volatile compounds such as NOx, N-Sorb cuts off essential components required for nitrosamine formation, effectively stopping the process before it begins. This action acts as a first line of defense, preventing the “fuel” for nitrosamine growth.
Scavenging Volatile Nitrosamines Post-Formation:
Some N-Sorb formulations can target volatile nitrosamines by adsorbing them onto their internal surfaces (porosity) or reacting with the nitrosamine and decomposing it in the headspace, reducing the concentration of these volatile nitrosamines in the packaging environment or in products. CSP’s technology can both neutralize these volatile nitrosamines as well as scavenge nitrosamine precursors to ensure nitrosamine levels are below regulatory thresholds.
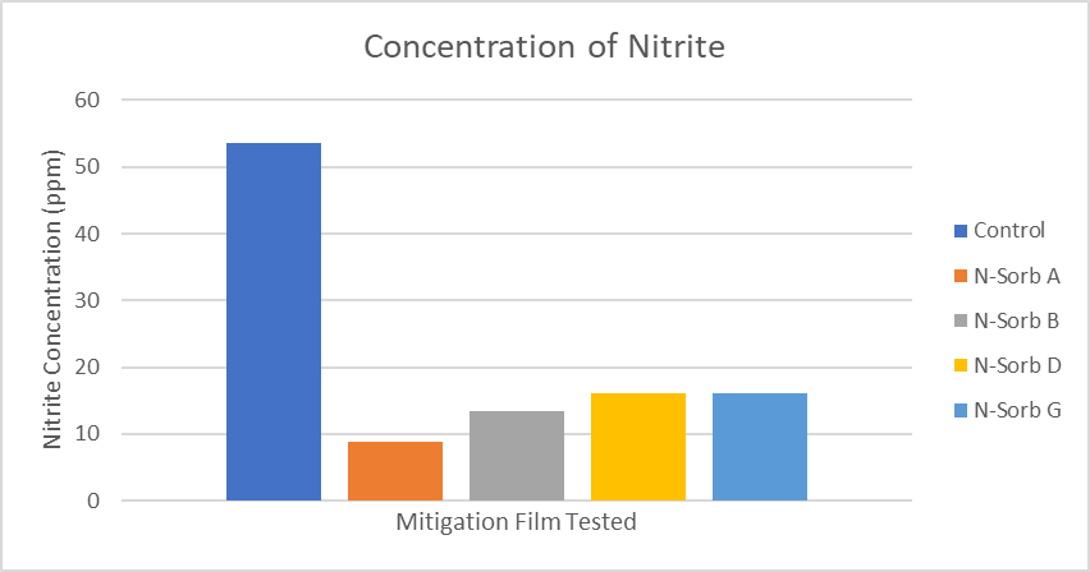
Nitrite adsorption in MCC tablets comparing N-Sorb films to control. Film and 3 MCC placebo tablets were aged 6 days at 60°C. N-Sorb delivered >70% drop in nitrite concentration versus control
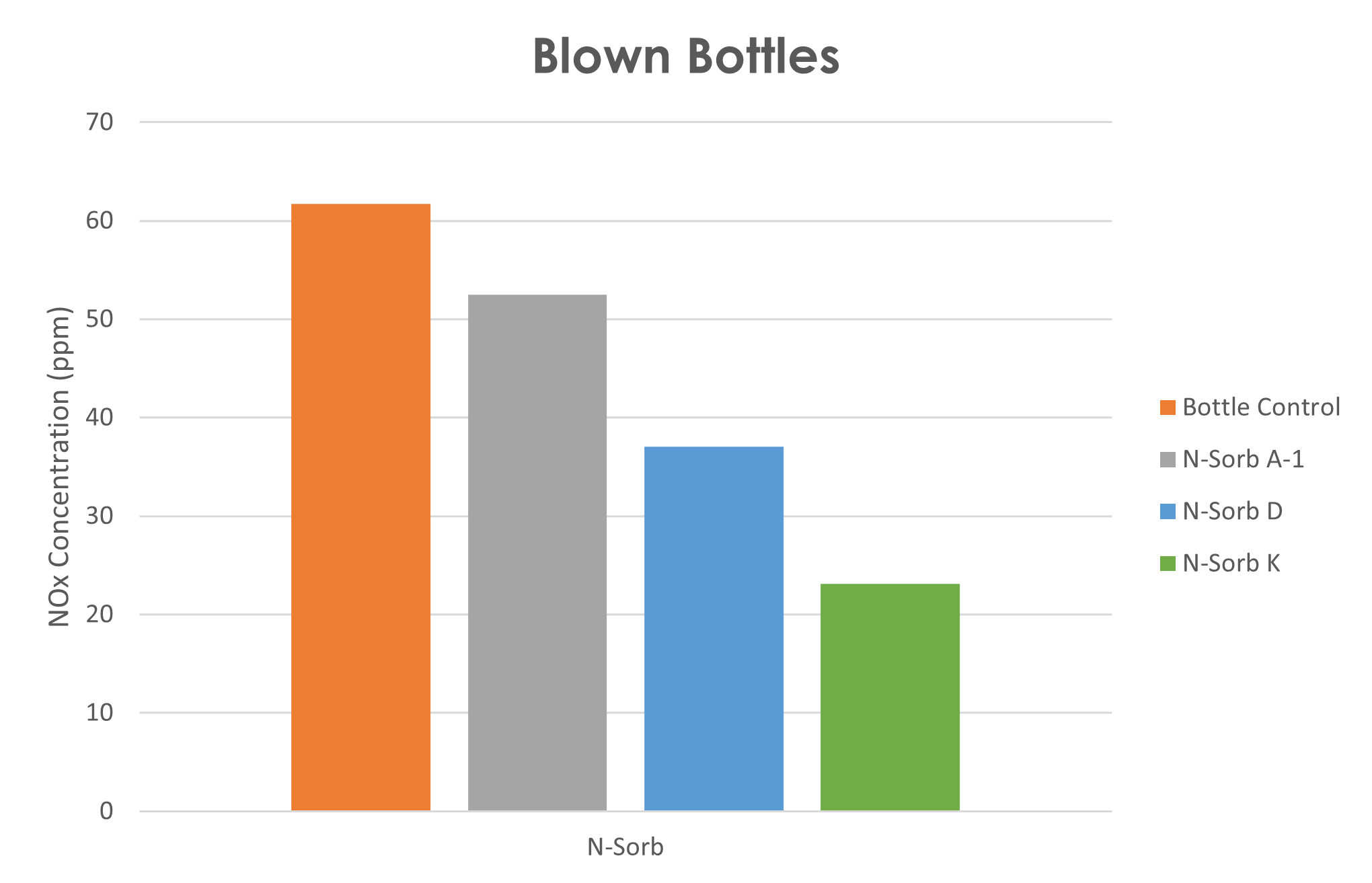
Nitrite scavenger (N-Sorb) placed in blown bottle and aged 6 days at 60°C shows N-Sorb K delivered 70% reduction in nitrite.
How is N-Sorb deployed?
N-Sorb can be deployed in various physical formats to seamlessly integrate into current packaging designs. The most common deployment method for oral solid dose drugs is as an Activ-Blister™ solution, which incorporates a piece of N-Sorb film into individual blister cavities to protect each dose from nitrosamine formation. Additional formats include injection molded canisters, blown bottles, and drop-in N-Sorb components.
How can N-Sorb help pharmaceutical companies comply with regulations?
Regulatory bodies like the FDA and EMA have set limits on acceptable nitrosamine levels in pharmaceuticals. N-Sorb assists companies in meeting these standards, enabling them to bring safer products to market while reducing the need for reformulation or costly adjustments.
Accepted into the FDA’s Emerging Technology Program (ETP), N-Sorb represents a significant innovation in pharmaceutical packaging. This acceptance allows Aptar CSP to work directly with the FDA, ensuring the development and validation of the N-Sorb technology meets and exceeds regulatory expectations. Pharmaceutical companies can confidently integrate N-Sorb into their products, assured of compliance not just with FDA nitrosamine impurity guidelines but also those set by authorities such as the European Medicines Agency (EMA), Health Canada, and the Pharmaceuticals and Medical Devices Agency (PMDA) of Japan.
Why N-Sorb Technology?
- Cost and Time Savings: Reduces or eliminates the need to reformulate to meet regulatory guidelines
- Maintain Brand Integrity: Minimize risk of recalls and associated negative impact to brand value
- Proven Efficacy: Data demonstrates strong evidence that N-Sorb effectively prevents nitrosamine formation and reduces nitrosamine levels post formation. Check out our series of technical papers below to view the data.
- Simplified Risk Management: Adaptable to various packaging forms and dosage sizes, easy to implement with minimal impact to manufacturing processes
- Expedite Speed to Market: Internal R&D capabilities and partnerships with CMOs facilitate rapid proof-of-concept testing and seamless integration into existing manufacturing processes
- Comprehensive Solution: Custom-engineered solutions address complex stability issues, including multiple nitrosamines with varying limits in a single drug product
- Regulatory Support & Alignment: CSP’s partnership with the FDA through the Emerging Technology Program can help streamline regulatory submission with N-Sorb. The technology aligns with the FDA’s latest guidance recognizing packaging changes as a possible solution for nitrosamine risk mitigation